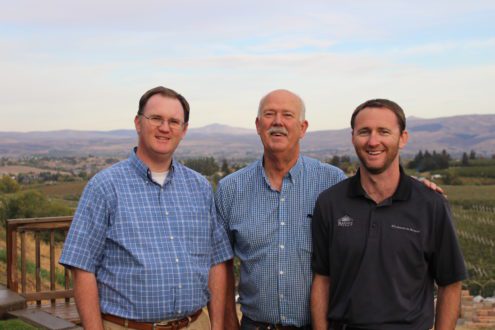
Jan 3, 2019Matson Fruit grows generational apple legacy In Washington state
The Matson family is credited with coming up with the 850-pound apple bin, but decades later, their willingness to try something different is again attracting attention from other growers.
One year ago, Matson Fruit finished gutting its apple packing line and installing an automated apple sorter. Four years ago, the company opened a robotic shipping facility that was described as the first of its kind in the industry.
The Matsons said tree fruit growers in the Yakima Valley of Washington state have few trade secrets, often sharing with each other know-how about growing apples, packing and selling them. They also will share information with the greater industry.
In October, an out-of-state reporter and a group of businesspeople from New Zealand got separate tours of the family’s fruit packing and storage facility in Selah, Washington.
The family has a history of innovation, starting with Sven Matson, who with his sons planted the family’s first orchards in the area.
“My great-grandfather was a little-tiny store owner in Chicago,” said Rod Matson. “Actually, he did immigrate from Sweden, he and his wife. They had the greenhouses in Chicago for a while, then they went to a little retail store and in 1907, he and a close friend of his, Mr. Sundquist took a trip out west.”
Sven Matson planted 80 acres in 1908 in the Selah Heights area. Water was carted up to the orchard by horse. Without a training system or a dwarfing rootstock, the apple trees grew 20 feet tall.
Later generations not only improved on growing techniques but also the packing process. Some of the details are lost to history, but by mid-century, the Matsons were credited with developing the larger 850-pound apple bins to replace smaller boxes.
“It was the third generation that did that,” said Rod Matson. “They built two bins the first year. They put two down, and it turned out OK, and the next year they built 50. Then the next year they built several thousand.”
It was a big change before the era of electronics.
“I guess when I look back at that, innovation was way different than today,” he said.


Packing it in
Today, Rod and his two sons are shareholders in Matson Fruit. While Rod and his son Jason are out in the field growing the fruit, son Jordan oversees the packing operation in downtown Selah for apples and pears, and also works closely with the sales desk at Rainier Fruit Co., which markets, sells and provides analytics for the Matsons and five other large independent growers in Washington. Matson cherries and winegrapes are packed elsewhere.
As production manager for Matson’s, Jordan Matson in recent years oversaw massive new projects to update the processing and shipping buildings in Selah – he declined to detail the costs of the projects, or even total acreage of the family’s orchards.


The Matson processing complex in downtown Selah is a mashup of history and innovation, where the oldest building is 94 years old but the newest, the robotic warehouse, is only four years old. The automated storage retrieval system cuts out a lot of human labor: Automated pallet cranes place each pallet into one of the 4,060 positions of the cold storage rack configuration where it will then be available to retrieve automatically by a warehouse management system, or when specifically directed by a user.
Other buildings, like the one that houses the new automated apple packing line, are somewhere in between. The building was built in 1994, but one year ago, Jordan oversaw gutting the facility, re-doing it and fitting it out with cutting-edge equipment.
While the pear line is more traditional, with a crew that hand-sorts the fruit for quality, the apple line now accomplishes the task with a digital system. Each apple traveling down a wide set of conveyor belts is photographed roughly 300 times from different angles using different types of light. Based on the photographs, the software program scores the apple for quality confidence and takes out apples with low scores.


The process from photography to removal takes place in roughly two seconds, and in just several feet of the assembly line. It’s a necessity of the building rather than a flourish of the electronic system. Jordan said he was limited in that the building was only so long and he needed an adequate number of drop points where the apples roll down toward packers. He was unable to purchase more land to make the building longer because a permanent rail line was located nearby. The solution was to take out the sorting table and replace it with a digital system.
Four years ago, building the robotic warehouse was also challenging. This time the limit was not space, but time: Jordan had little more than a year to firm up designs and build the plant after the old shipping facility they had been renting was purchased by a new owner.
Deadlines were persistent, and problems came up during construction.
“Dealing with Austrian technology, German conveyors, American design folks across the United States, (the) Washington State Department of Labor and Industries – which has some really weird electrical rules and laws which meant the Austrians couldn’t do any of their own electrical work – it was interesting, just really interesting,” Jordan Matson said.
Rod Matson recalled how he has questioned some of Jordan’s ideas.
“Nobody’s got one. Will it work? Will it be economic?”
Ultimately, he said, “we really took a little leap of faith.”
And, he adds, it worked.


Growing smarter
Like other apple growers, the Matsons have had to also evolve their farm practices to meet demands for specialized varieties, comply with modern labor rules and use technologies that their neighbors have adapted.
As growers, the Matsons have orchards around the bedroom community of Selah, in the greater Yakima Valley, and in the Mattawa area, which is about an hour’s drive east of Selah. About 80 percent of their crops are apples, although there also are some pears, cherries and winegrapes. They grow quite a mix of apple varieties, and in the spring of 2017 put in their first blocks of Cosmic Crisp, the much-anticipated variety restricted to growers in Washington state.
Jason Matson said so far, they’ve tried growing Cosmic Crisp in a steep-V trellis system.
“It certainly has its place in the harvest window, with it being a late-season apple,” Jason Matson said. “One of the expectations is to meet a harvest window: That late Golden Delicious, early Red Delicious timing, as those varieties continue to decrease.” He added that since Cosmic Crisp stores well, it likely will also fill some of the space vacated by Red Delicious.
In early October, Matson Fruit was finishing construction on H-2A-compliant worker housing – buildings that each house up to 12 people.


The cost of construction comes out to about $10,000 per person. “We’re farmers that build housing,” said Rod Matson. “Either you do this, or you don’t get your work done. It’s pretty expensive to not get your work done.”
Yakima Valley apple growers are close-knit group and discuss such industry-wide challenges together often. It’s not uncommon for the growers to share expertise in a certain area, or share their results for something new they’re working on.
“In this region anyway, all the fruit growers are very close,” Rod Matson said. “It’s a pretty special thing to me.”
– Stephen Kloosterman, FGN Associate Editor
Top photo: Jason, left, Rod and Jordan Matson are shareholders in Matson Fruit. Photos: Stephen Kloosterman